A clean basis for individual painting processes
Current BvL system projects as convincing contributions for the requirements range for PaintExpo
In the field of industrial cleaning in preparation for individual painting processes, system manufacturer BvL Oberflächentechnik recently implemented various solutions for a range of different customer requirements.
Comprehensive cleaning process with high throughput
Within its production process, a large European manufacturer of household appliances cleans different oven components using a total of three newly installed YukonDAH continuous systems in combination with an existing overhead conveyor system. After washing and drying, the components have to be free from oil, dirt and residual moisture, which also applies to folded edges and undercuts. This ensures optimum preparation for the subsequent enamelling process. The 3-cycle tank system executes to following processes consecutively: cleaning, pre-rinsing, post-rinsing, air blasting and drying. Each one of the almost 30 meter long systems allows a total throughput of approx. 1.6 million cleaned oven components per year. To save energy, the extraction management minimises the volume of exhaust air and the optimised flow reduces the required heating output.
Demand-based cleaning of heavy metal parts before painting
Another example from the current system range will be delivered to the customer shortly. In preparation for subsequent painting, the planetary gears, slewing gears and winches at a large metalworking company are cleaned and phosphated, then rinsed and dried with circulating air in a PacificDTH cycled system. The components move through the system which is linked to the customer’s overhead conveyor system. The two oscillating special nozzle systems, which are separately connected to the washing and rinsing tank, ensure reliable cleaning results and surface properties within the same chamber. The large system allows treatment of large components with an edge length of up to 3 metres. The additional insulation on pipes, filters and tank covers and the use of a steam condenser ensure a significant reduction of the energy consumption.
Libelle sensor technology offers predictive maintenance
On both cleaning systems, different Libelle sensor equipment ensures continuous monitoring of the cleaning medium to reduce the maintenance effort.
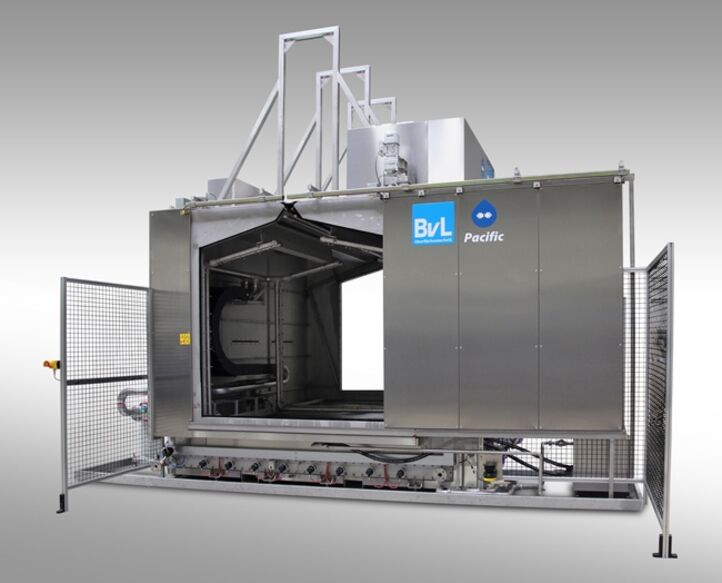
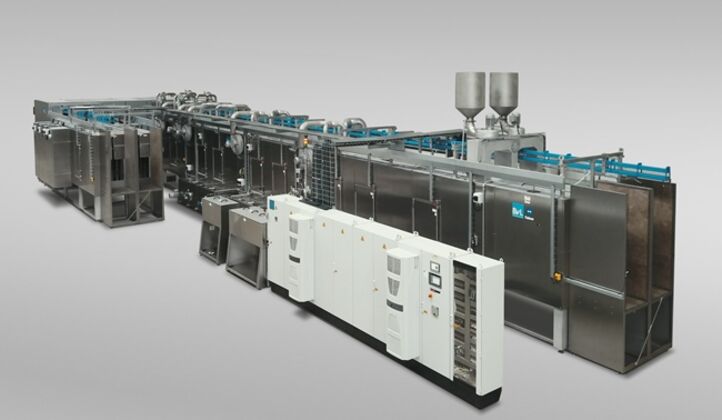
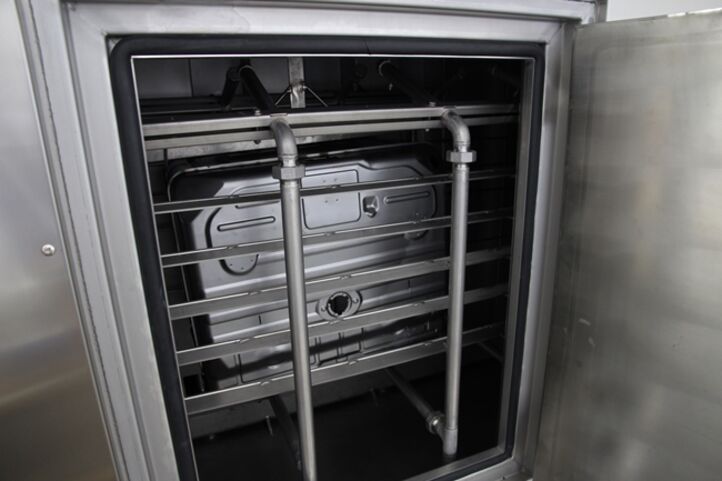