Cleaning line with 5 stations allows for short cycle time
BvL cleaning line quickly makes engine components usable again
Oil, grease, carbon residue, rust – during the reconditioning of truck engine components, these have to be removed thoroughly and the components have to be available again quickly. A large automotive supplier in southern Germany was focused on a particularly short cycle time for the reconditioning of complete engines. BvL Oberflächentechnik solved this task by cleverly linking several cleaning, drying and cooling stations.
Modern internal combustion engines in commercial vehicles have to be economical and powerful, produce low emissions and achieve very high mileage figures. That means that reconditioning of used engines also requires maximum cleanliness. In this case, the key project targets were to achieve the ambitious OEM cleanliness requirements, in particular in the hard-to-reach channels for air, oil, water and fuel in connection with the high throughput.
Automation of the cleaning line eliminates operator interventions
BvL Oberflächentechnik overcame this challenge with a complex cleaning line. The system concept includes pre-cleaning and fine cleaning as well as drying and cooling. The multi-chamber design of the cleaning system allows for a high throughput. In addition, the system parts are linked, so that no operator interventions are required after loading.
Simultaneous loading of parts in five stations with discharge option
The system comprises a total of five stations where the parts are treated at the same time. The first step is a NiagaraRH 1600 cleaning system for pre-cleaning. As this process step generates a high contamination load, this station is equipped with two independent tanks. When one tank is empty, the system can switch to the second tank. This means that a bath can be changed during active operation without having to interrupt the process or the automation. After pre-cleaning, the parts can be transported to a discharge station. The operator decides beforehand whether only pre-cleaning is required. In this case, the parts are provided to another process (e.g. blasting) after cleaning and are then introduced back into the line for the additional, final cleaning process. Fine cleaning is carried out in two NiagaraDFS 1200 cleaning systems. This multi-chamber design makes the required high throughput possible while offering redundancy.
The NiagaraDFS is a flood/spray cleaning system with revolving wheel technology. The rotation of the goods to be cleaned around the horizontal axis ensures thorough cleaning, supported by an ultrasonic device. After the actual cleaning, the parts move to a NevadaVTR 1200 continuous vacuum dryer. At the end, the parts are cooled to the required temperature in the Arctic cooling tunnel. The BvL Smart Cleaning Apps enable intelligent cleaning and digital linking. Transparent process information makes predictive diagnostics and maintenance possible.
Information available at AMB and Parts2clean in Stuttgart
BvL Oberflächentechnik will be exhibiting at the trade fairs AMB (September 13 to 17, 2022) and parts2clean (October 11 to 13, 2022) in Stuttgart and will be providing information on cleaning solutions and innovative concepts for different industries and requirements. Washing trials with original components can be carried out at the in-house technology center in Emsbüren. These trials determine the economically and ecologically ideal combination of plant technology, cleaning medium and program sequence for the specific customer.
AMB: Hall 5, stand 5C84
P2C: Hall 4, stand A10
BvL Oberflächentechnik GmbH is one of the largest suppliers of water-based industrial cleaning systems in Germany. As a system partner, BvL offers comprehensive customer solutions through integrated services – from compact washing units and filtration/automation solutions to complex large projects with process monitoring, always complemented by reliable service. BvL currently has around 160 employees. In terms of exports, the company has expanded its position on an international scale and can rely on an extensive sales and service network in 20 countries.
Contact:
BvL Oberflächentechnik GmbH
Grenzstr. 16
48488 Emsbüren Germany
Tel.: +49 5903 951-60
Fax: +49 5903 951-90
info@bvl-group.de
www.bvl-group.de
Press release:
Christine Brühöfner
Marketing
Tel.: +49 5903 951-509
Fax: +49 5903 951-90
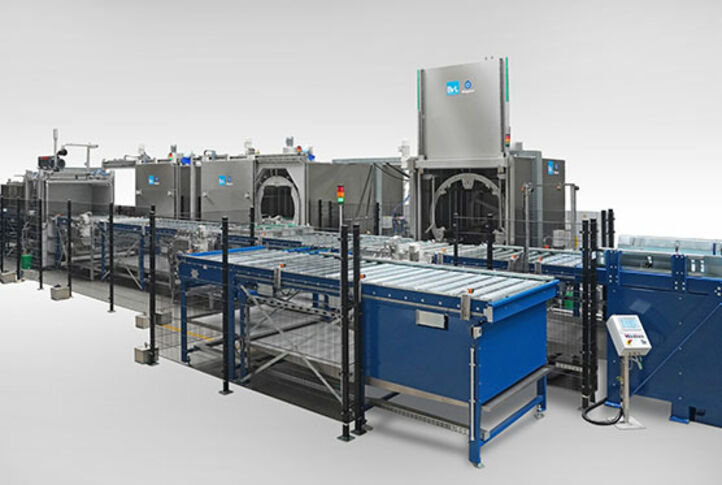
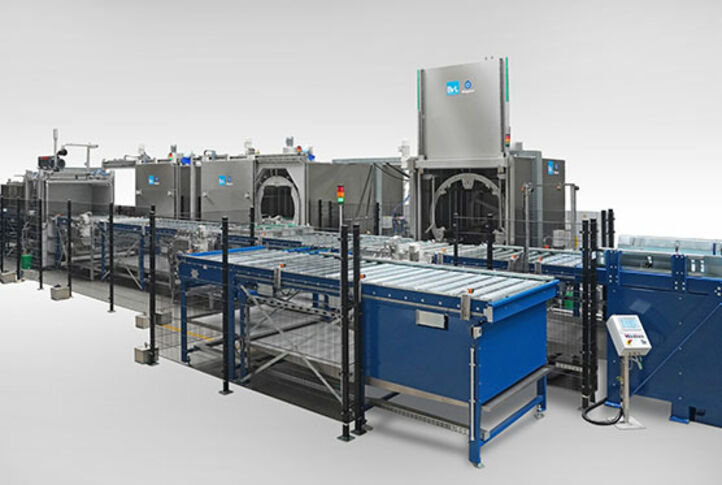
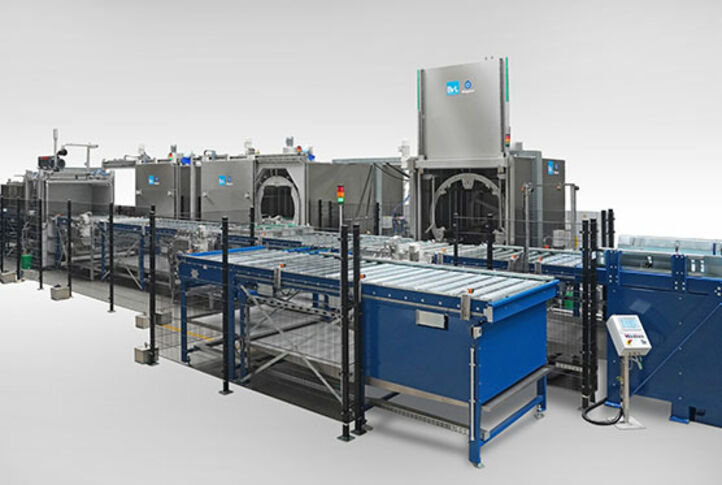